Un paso necesario para obtener el máximo rendimiento de tus máquinas CNC es optimizar las condiciones del proceso de corte en tu centro de maquinado, centro de torneado, fresadora CNC o torno CNC.
Existen muchos factores que debes controlar para eficientar tu producción con maquinaria CNC. Este artículo aborda estrategias recomendadas para optimizar los parámetros de corte y su relación con el desgaste de la herramienta y la potencia del proceso, enfocándonos en aquellos aspectos que generan un impacto tangible en tus operaciones.
¿Por qué es recomendable optimizar los parámetros de corte?
En tu taller CNC, el tiempo vale oro: el costo del alquiler del local, la mano de obra, la renta o depreciación de la maquinaria, son gastos que debes cubrir periódicamente. Mientras más piezas puedas producir por día, por hora o por minuto, más rápidamente cubres tus costos fijos y mayor será tu ganancia. Pero si al aumentar la rapidez de maquinado los parámetros de corte no son adecuados, la herramienta de corte sufrirá mayor desgaste, se utilizará más energía eléctrica y se elevará el costo por pieza. Por consiguiente, una vez que tienes la pieza montada en tu equipo CNC, el objetivo es remover la mayor cantidad de material con las condiciones óptimas para producir con el menor costo posible.
¿Qué parámetros de corte optimizar?
La tasa de remoción de material TRM (conocida en inglés como MRR por Material Removal Rate) es un número que indica la cantidad de material por minuto que se remueve durante el maquinado. Por sencillez, plantearemos el cálculo para el caso de un torno CNC:
TRM = π x Dm x N x ap x f = Vc x ap x f
Donde:
- Dm es el diámetro promedio del inicio (Di) al final (Df) de la operación (mm).
- ap es la profundidad de corte (mm).
- f es el avance por revolución (mm/rev).
- N son las revoluciones por minuto (RPM) de la pieza.
- Vc es la velocidad superficial de corte (m/min).
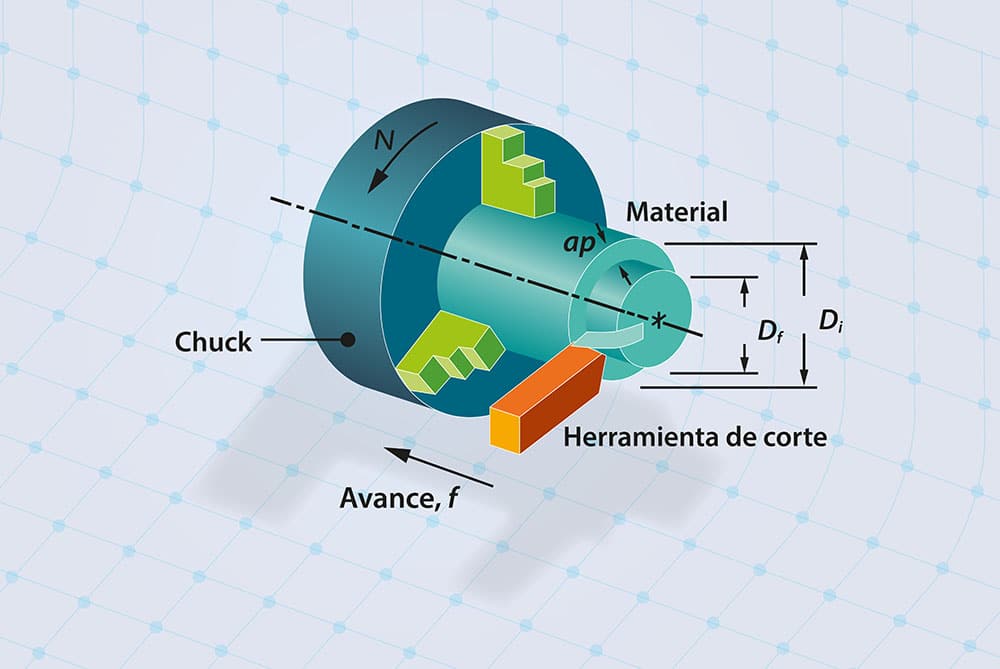
Para aumentar la tasa de remoción de material, podemos incrementar las RPM (N), la profundidad de corte (ap) o la velocidad de avance (f), cada una con efectos diferentes en el rendimiento de la herramienta y el resultado final del maquinado.
Influencia de las RPM
Aumentar las RPM del husillo es una manera rápida de incrementar la TRM, pero también puede acelerar el desgaste de la herramienta. Al aumentar las RPM, se incrementa la velocidad superficial de corte (Vc = π x Dm x N), lo que genera mayor temperatura y puede reducir la vida de la herramienta. Como lo muestra la gráfica siguiente, a mayor velocidad superficial de corte, menor vida de la herramienta (medida en metros).
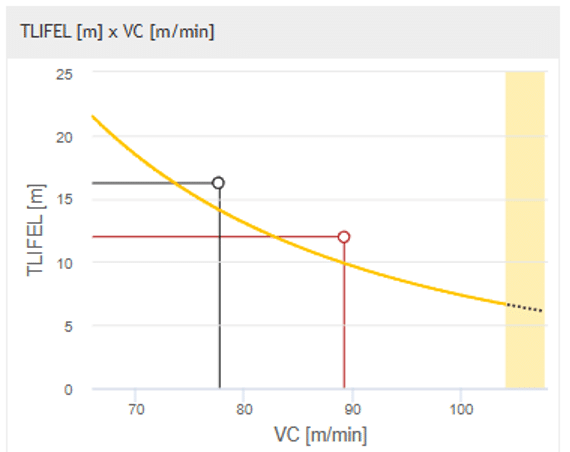
Sin embargo, para ciertos materiales, las herramientas con recubrimiento (como TiAlN en herramientas de carburo), permiten aumentar la velocidad superficial dentro de un rango óptimo, logrando reducir el desgaste adhesivo y mejorar la evacuación de calor. Con otros materiales como el aluminio puede ser preferible usar herramientas sin recubrimiento. Por lo tanto, es recomendable verificar las especificaciones del fabricante de herramientas para evitar un desgaste prematuro.
Influencia de la profundidad de corte
Aumentar la profundidad de corte (ap) dentro de los límites recomendados por el fabricante puede aumentar significativamente la TRM y reducir el tiempo total de maquinado sin detrimento en la vida de la herramienta. Una mayor profundidad de corte requerirá menos pasadas y menos tiempo desperdiciado en movimientos de reposicionamiento.
Consideraciones clave:
- Potencia de la máquina: Un incremento en la profundidad de corte demanda mayor torque y potencia, lo que puede superar la capacidad del husillo o de los servomotores en máquinas pequeñas.
- Rigidez de la máquina: Una profundidad de corte excesiva puede inducir vibraciones y afectar la calidad de la pieza.
- Vida de la herramienta: En algunos casos, aumentar la profundidad de corte puede prolongar la vida útil de la herramienta si se equilibra correctamente con la velocidad de avance y la refrigeración. No obstante, utilizar valores inferiores a los recomendados puede provocar desgaste irregular y acabados deficientes.
Influencia de la velocidad de avance
La velocidad de avance (f) afecta principalmente la rugosidad superficial de la pieza maquinada. Tanto un avance demasiado alto o bajo puede generar marcas visibles en la pieza, al cambiar la forma de la viruta, generando vibraciones que pueden afectar la durabilidad de la herramienta. Un avance demasiado alto puede romper la herramienta por impacto excesivo, mientras que uno bajo puede causar rozamiento y deformación en vez de corte de viruta, provocando un desgaste del filo. La velocidad de avance debe armonizarse con la velocidad superficial de corte.
Consideraciones clave:
- Para torneado, utilizar herramientas con radio mayor o geometrías “wiper”, que permiten velocidades de avance más altas sin sacrificar el acabado.
- Para fresado, optar por herramientas con ángulo de hélice variable puede ayudar a reducir vibraciones y mejorar la penetración vertical.
- Emplear herramientas con recubrimientos de baja fricción para reducir el desgaste y mejorar la estabilidad del proceso.
Recomendaciones y conclusión
Antes de dedicar tiempo a optimizar el proceso de corte, es fundamental considerar el tamaño del lote de piezas y los procesos previos y posteriores al maquinado. Con frecuencia se invierte más tiempo en el montaje y ajuste de la pieza y herramientas que en el tiempo de corte de una herramienta en particular.
En muchos casos, los fabricantes de herramientas indican el rango adecuado para cada parámetro de corte, lo que permite seleccionar valores óptimos sin necesidad de realizar pruebas extensivas.
Consulta el sitio web del fabricante de herramientas. Por ejemplo, Sandvik Coromant ofrece una herramienta digital (CoroPlus Tool Guide) para seleccionar herramientas y condiciones de corte, proporcionando estimaciones sobre la vida útil de la herramienta y el consumo de energía.
La optimización del proceso de corte comienza desde la elección de la herramienta adecuada según el material y la máquina CNC disponible. Herramientas de alto rendimiento pueden requerir máquinas más robustas, mientras que en equipos de baja potencia se pueden usar estrategias como corte trocoidal o herramientas de menor radio de punta para mejorar la eficiencia.
Ajustando correctamente los parámetros de corte, se pueden lograr procesos de maquinado más rápidos, eficientes y rentables. ¡Optimiza el uso de tu CNC y mejora la productividad de tu taller!